Probably, you are wondering what a wire rope is, its functions, features, classification criteria, or applications.
In this guide, you will find all the information you are looking for about wire ropes. So, before buying your next wire rope, read this guide.
What is Wire Rope
A wire rope is a line designed with metallic wires. These individual strands of wires are warped together in a helical pattern to form a strong cord. Besides, these wires are twisted around a solid center.
This rope is designed to withstand high amounts of bending stress making it ideal for applications that involve industrial heavy lifting.
The supporting core coupled with the reinforced wires makes it an ideal and superior support tool
Also, the most common material used to manufacture these ropes is pure steel with a carbon content of 0.4 percent.
Numerous individual strands are wrapped around a single-piece core in a way that creates a helix pattern. The diameter of the rope is determined by the number of strands used to create the wire rope.
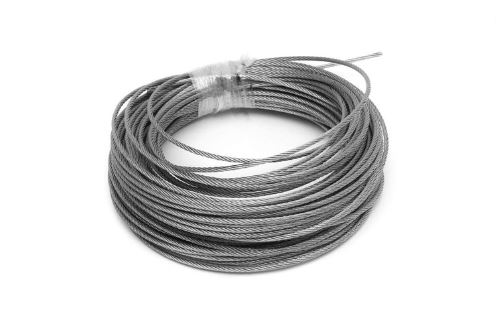
Features of a Wire Rope
There are key features incorporated into the design of the wire rope to ensure that it provides steady support when utilized. These features include;
- Wire ropes are classified according to strength which denotes its maximum load-bearing capability. This is typically given in tons and is vital as it will help you select the most suitable wire rope for your needs.
- Wire ropes are equipped with reserve strength that is independent of the main strength classifications. This feature takes into account prolonged use which may result in wear as well as corrosion of the wire. It reinforces the wire allowing it to remain functional even under these conditions.
- These industrial cables are fortified with resistance to metal loss and deformation which is essential as it is designed for applications that involve a lot of strain. This feature is therefore important as it not only ensures durability but it helps lengthens the wire’s service life.
- The supporting cable is designed to be resistant to crushing. This feature fortifies the wire against pressure or other suppressing force. It can therefore easily withstand being put under strain.
- It also has fatigue resistance that allows it to be utilized multiple times over a period without succumbing to damage. Fatigue resistance also ensures that the wire can be used for a long time without risking breakage.
- The design of the rope factors in its ability to bend. A quality wire rope should be able to withstand bending in any direction without forming kinks or any other kind of deformities.
Benefits of Using a Wire Rope
There are multiple advantages to using the wire rope. These benefits include;
- Wire ropes are incredibly strong and can be used for a variety of industrial applications. Its capacity is gauged in tons making it ideal for a wide range of applications.
- The reinforced cable is resistant to stress, corrosion, fatigue, and wear. This ensures that it has a long service life
- This rope is typically coated with other materials such as PVC to enhance stability as well as improve its resistance to abrasions which is likely to be encountered in its various applications.
- It is a lightweight and highly portable cable which makes it easy to maneuver and install. Despite its small weight, it handles impressive weight.
- The wire rope is relatively cheaper compared to equipment used for similar purposes. It is also low-maintenance while durable making it economical.
- It does not require expert help to operate and can be easily used by anyone.
Components of a Wire Rope
Wire ropes are composed of our main components. These include;
· Wires
The main component of these cables is the individual wires designed from a multitude of different materials including bronze, steel, iron, Monel, and stainless steel. The different materials have unique features that make each of them suitable for different applications
These wires are produced with various beneficial properties that contribute to the overall high performance of the wire. These properties include resistance to fatigue, corrosion, and wear as well as its strength.
Strands
Strands are a combination of multiple wires warped together. They comprise varying numbers of wires and a wire rope can contain multiple strands depending on the intended use. There are three main configurations commonly used
- Single Layer: All the strands that make up the wire rope in this category are arranged in one level. The most used design in this category is the seven-strand wire rope. It involves a center strand surrounded by six additional strands around it.
- Seale: This design incorporates a double layer of strands around a center. Each layer has strands of similar diameter. The inner layer consists of smaller strands and the outer layer stands that lay in between the creases of the inner layer making a compact and sturdy design.
- Strand Core: The core strand is designed to maximize support and is sometimes also referred to as the independent wire rope core. It comprises several wires moulded together to create a helix shape strand
Core
This is the center prop of the wire rope which consists of multiple wires bound together. It is incorporated to function as a support feature. There are different types of cores;
- Fiber Core: This is designed using polypropylene a synthetic material or from different organic fibers. They have an increased resistance to fatigue and are also very flexible. Fiber cores improve the wire ropes braking load but have a lower crush resistance.
- Independent Wire Rope Core: This design is composed of a complete wire rope that may sometimes vary from the external strands. It incorporates an entire wire rope as a core making it ideal for industrial applications that involve handling heavy loads.
- Strand Core: Strand consists of independent wires twisted together to form a strand. The wires that make up the strand are designed from various materials. They are also manufactured in various lengths for different wire ropes.
Types of Wire Ropes
There are three major categories of these support ropes. These categories include;
Stainless Steel Wire Ropes
Stainless steel is the most preferred material thanks to its superior qualities. It has a remarkable resistance to corrosion and wear. It is also very strong and durable and can withstand high temperatures. These properties widen the field of application that the wire rope can be used in.
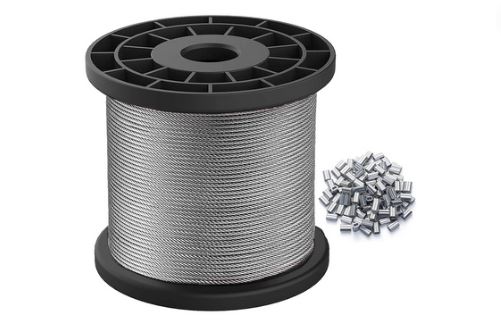
Galvanized Wire Ropes
This category contains wire ropes designed using carbon steel. Carbon steel has remarkable strength which makes it ideal for industrial applications. These industrial cables are coated with zinc to increase their limited resistance to corrosion. The material is also durable.

Coated Wire Ropes
The last category is coated wire ropes. These are wires manufactured using other materials like bronze iron or even steel. Their main defining feature is the protective external layer that they are coated with. Materials such as rubber or polymer are used as coats to increase their resistance to abrasion while keeping the cable intact.

How to Select the Best Wire Rope
Wire ropes are designed using different materials that are warped in various configurations. Therefore, not all wire ropes are suitable for any applications. When purchasing a wire rope you should consider the following factors.
- The environment: The type of environment is a vital factor to consider as it will directly affect the durability and longevity of the wire rope depending on the variety you have. For example, for environments with corrosive elements such as salty water the stainless steel wire rope would be suitable as it has a corrosion resistance. On the other for industrial applications that involve heavy-duty hauling the carbon steel wire cable would be ideal as it has remarkable strength.
- Flexibility: wire cables are often used to lift or support heavy objects. Different applications require different forms of support and some may require wrapping the wire around an object to provide support as well as stability. In such cases, it is important to ensure that you purchase a rope that can withstand bending by being flexible.
- Crush resistance: for applications that occur in small spaces and require handling of heavy loads the crush resistance is one of the factors you should look out for. This feature determines how much pressure a wire rope can handle while being pressed on.
- Strength: these industrial cables are designed for heavy-duty applications. The strength of the rope is a vital factor that can limit or even lead to damage to the cable and the contents it supports if overlocked. Wire ropes typically indicate the strength denoted in tones. The figure stands for the maximum weight the rope can support. It therefore best to select one that can handle its intended use.
- Abrasion resistance: the environment and the application will help determine the appropriate level of abrasion resistance required. Wire ropes with a larger diameter are better suited to withstand higher levels of abrasions while smaller ropes will be less resistant.
- Bending fatigue resistance: if your application involves repeatedly wrapping the wire rope at various angles then you should consider its fatigue resistance. The total number of wires used to make the rope determines how much fatigue it can handle. The thicker the cable the more fatigue it will tolerate. Its rotation resistance should also be considered.
- Elongation: The maximum elongation length ought to be taken into account. Depending on the application the wire is going to be utilized for you can go for a wire with enhanced elongation to better address your needs.
- Cost: Ensure that the wire cable you select is economically feasible. While more expensive wire ropes are of better quality they may not make sense for a small-scale operation that only handles limited goods. However, for large-scale operations that handle heavier goods, a quality durable wire rope will be more economical in the long run.
Maintenance of a Wire Rope
Maintenance of your rope is an important activity that ensures that you fully utilize your rope while maintaining its peak state. It also prolongs the service life of your wire rope.
- You should lubricate your wires at a six-month interval. Lubrication is vital as it minimizes friction and limits wear. This helps to prolong its life.
- Thorough inspections should be conducted to identify any signs of damage. While inspecting you should look out for signs of corrosion, kinks, breakage, and wear. This is an important safety assessment as it ensures that there are no accidents caused by faulty wires.
- Inspect the movement of the sheaves and ensure they are fitted in the appropriate groove size. It will ensure that they are protected from vibrations and abrasions. The sheaves should also be lubricated and regularly cleaned
- Storing the wire rope in a protected place is also an essential step in preventing corrosion and other potentially damaging elements. The storage area should be dry, well-cleaned, and ventilated to prevent moisture from building up. When considering long-term storage, you should grease it at set intervals and turn it every once in a while to prevent unevenly distributed grease.
Possible Defects of a Wire Rope
There are common problems likely to be encountered when using a wire rope. The most common defects include;
Broken Wires
This can be caused by several issues. The typical causes of broken wires include;
- Fatigue caused by repeated usage
- A collapse in the diameter of the rope is caused by a malfunctioning core
- Corrosion is another factor that often leads to damage to the wire rope cross-section.
- Incorrect spooling may result in the formation of kinks that lead to breakage.
- Waves forming due to repeatedly bending the rope may develop into breaks
Corrosion
Corrosion is a common occurrence for galvanized ropes. Extreme cases may result in breakage of the rope. Corrosion can occur both internally and externally which may result in a reduction in the surface area of the rope. It also reduces the strength of the rope.
Deformation
These deformations can be a result of waves, kinks, or settling. Deformation that is the result of settling limits the elasticity of the wire rope as time progresses. Kinks are a result of existing loops getting tightened as the rope is utilized which unbalances the length of the rope leading to a decrease in the length of the rope.
Abrasion
Several factors can cause abrasion on the wire rope. These factors include improperly lubricating the wire rope during maintenance. A worn-out sheave or if the sheave is corrugated. Contact with other suitable objects may also result in abrasion. The ultimate damage caused by abrasions starts with small and dismissible flat spots. If not properly addressed over time the affected area wears further leading to irreparable damage.
Other possible causes include:
- Incorrect rope size
- Wrong fleet angle
- Poor spooling
- Frozen rollers
- Tension
Sizing of a Wire Rope
Sizing a wire rope is an important step before committing to a purchase. Incorrect sizing may lead to a malfunction or unsuitable wire rope that will fail to perform its expected roles. It is therefore important to ensure that you select the most appropriate size that will provide you with the best service. When sizing you should consider the following factors;
Diameter
This unit denotes the biggest cross-section of the wire rope. It takes into account the complete circumference of the rope. The commonly used units are inches and millimeters. It is also important to note that most manufacturers that deal with wire rope lean towards a soft conversion which means an inch will the equated to 26mm as opposed to the actual value which is 25.4mm.
Construction
These industrial support cables are designed using multiple individual wires that are twisted to construct an individual rope. Sizing encompasses the number of wires and strands as they directly impact the overall performance of the wire rope. This parameter can be represented by multiples like 6 x 9 which means that the rope is comprised of 6 strands that are composed of 19 strands.
Breaking Strength
The thickness of the wire rope is directly proportional to its break strength. This is the compilation of the cross-section of all the wires which constitute. This parameter is vital as it determines the load-bearing capabilities of the wire rope as well as its durability. The breaking strength of the wire rope also determines the safety of operating conditions.
Applications of a Wire Rope
The remarkable strength and versatility of the wire rope make it suitable for a variety of applications. These applications include;
- Construction: lifting machinery, heavy loads, cement blocks, and, suspending equipment
- Energy generation: construction of solar parks and wind turbines power and systems designed for transmission and distribution.
- Leisure applications: swimming pools, sports facilities, and amusement parks.
- Mechanical engineering: different manufacturing processes, moving heavy loads, assembly lines, and conveyor systems
- Metal industry: mining, smelting, and the production of other raw materials such as steel, copper, and aluminum.
- Aerospace: aircraft cockpits, space exploration, and aircraft rigging.
- Infrastructure: construction of pedestrian, highway, pipeline, and suspension bridges.
- Entertainment: used in movie sets to move items, assist in stunts, and support temporary structures.
At Guofeng, we offer you the best wire ropes in the industry. Our wire ropes come in different lengths and diameters depending on your unique specifications.
More Resources:
Stainless Steel Wire Rope – Source: GUOFENG
Wire Rope – Source: IQS Directory
Galvanized Wire Rope – Source: GOUFENG
Wire Strands – Source: Science Direct
Steel Wire Rope – Source: GOUFENG